- Explore our industry expertise
- Success stories
- Schinko boosts productivity by 20%
Schinko boosts productivity by 20%
20% higher productivity
Transparency motivates and reveals opportunities for optimization
Information in real time
Live feedback on work progress makes planning and logistics easier
Reduction in set-up times
Machine dashboards promote fast response and better cycle times
Challenge
What to do with the data?
Data, data, data... To improve in many areas and create transparency, Schinko's employees used to spend a lot of time collecting endless data: energy, gas and coolant consumption, machine running times, fault reports, material purchases, delivery times and much more. But collecting and evaluating the data became too much effort compared to productive work. Excel spreadsheets overflowed, and employees could no longer keep up. That was a good three years ago. Schinko's management started looking for alternative solutions in order to take a major step towards digitization. Requirements:
- Collection of data from different machines, manual workstations and software systems
- Creation of logical connections between different data sources
- Building of meaningful dashboards with extensive manufacturing information
- Continuous comparison of planned and actual status
- Integration of more and more business areas
Engagement
Start: Proof of concept
It all began with a proof of concept, which included an architecture and integration concept as well as a functional prototype. Experts in lean management and digitization from GFT, therefore, analyzed Schinko's various production areas. The company produces high-quality, customized sheet metal enclosures for many different industries, including semiconductors, medical technology, metrology and 3D printing. Production is divided into five areas: cutting of sheet metal blanks, edging, welding and grinding, nano high-tech powder coating and final assembly. Some production steps, such as laser cutting and coating, are relatively automated, while others, such as bending of sheets, grinding and final assembly of parts, are hard manual work. They all need to be digitized.
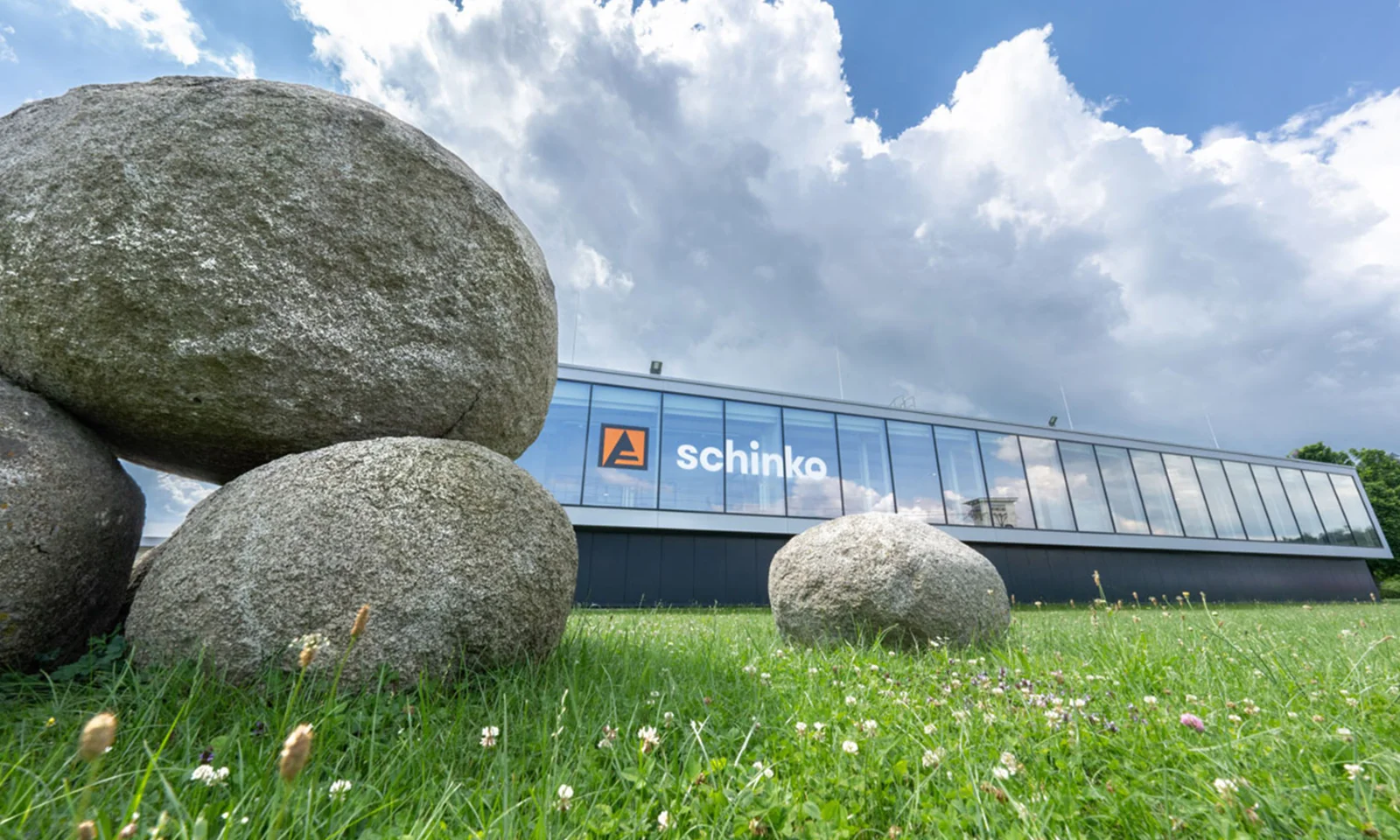
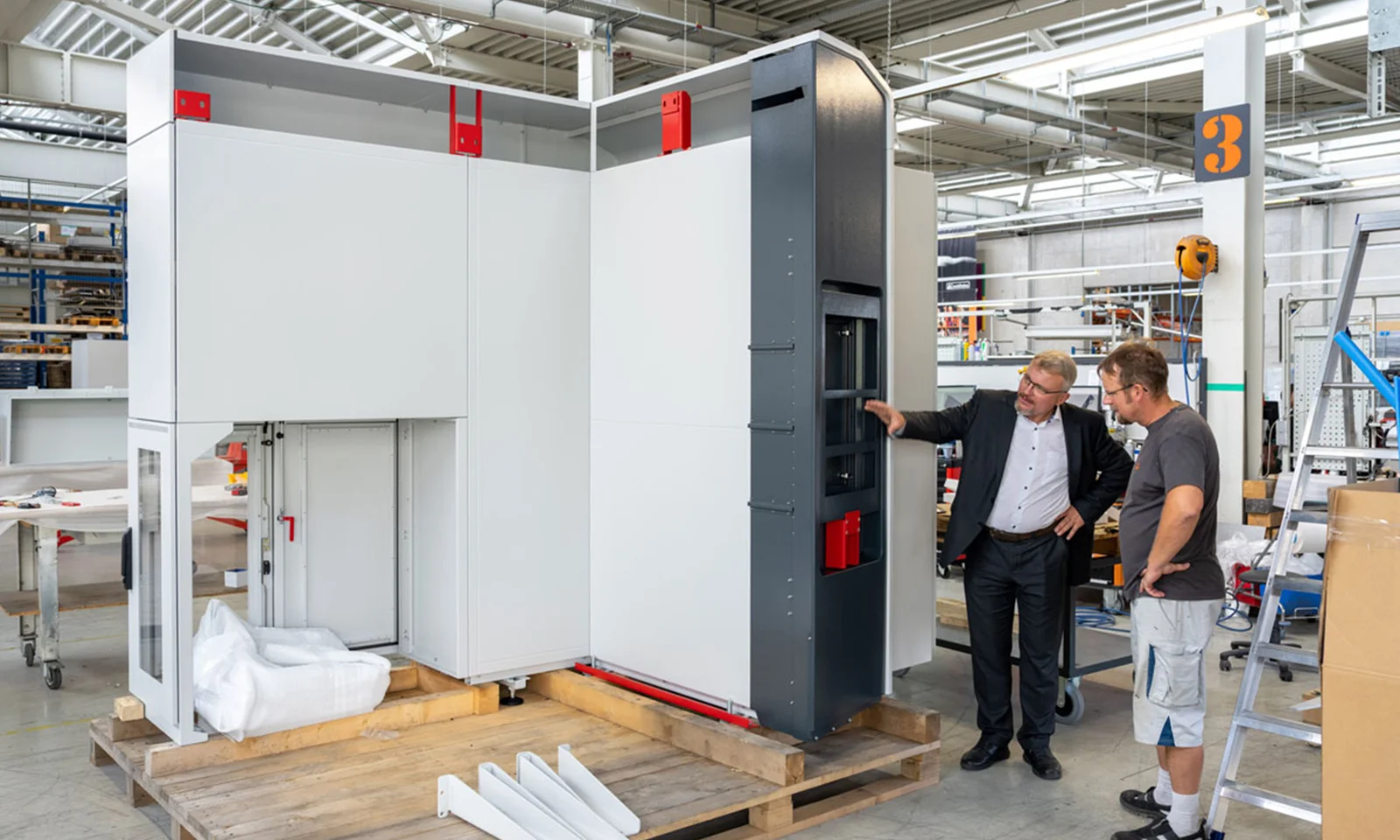
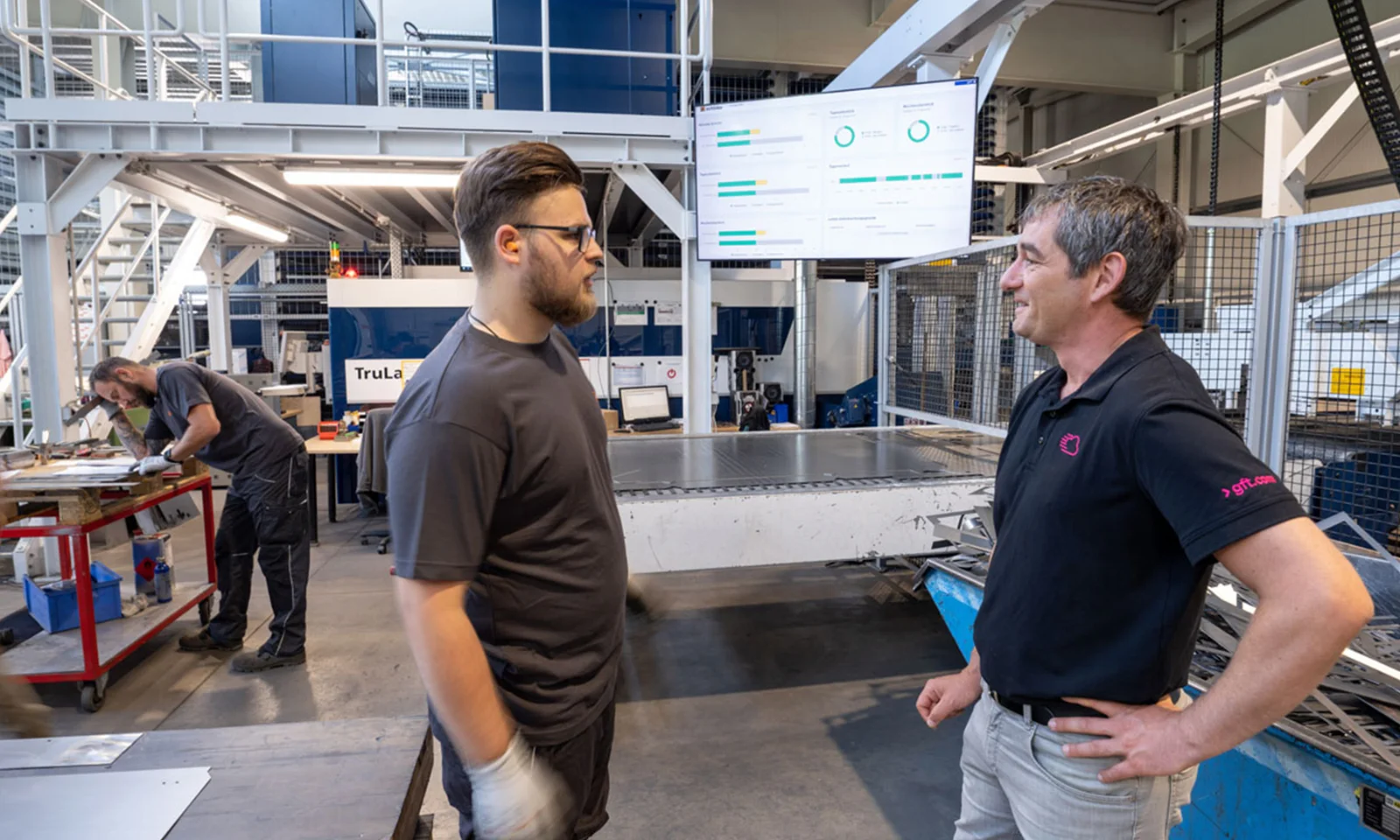
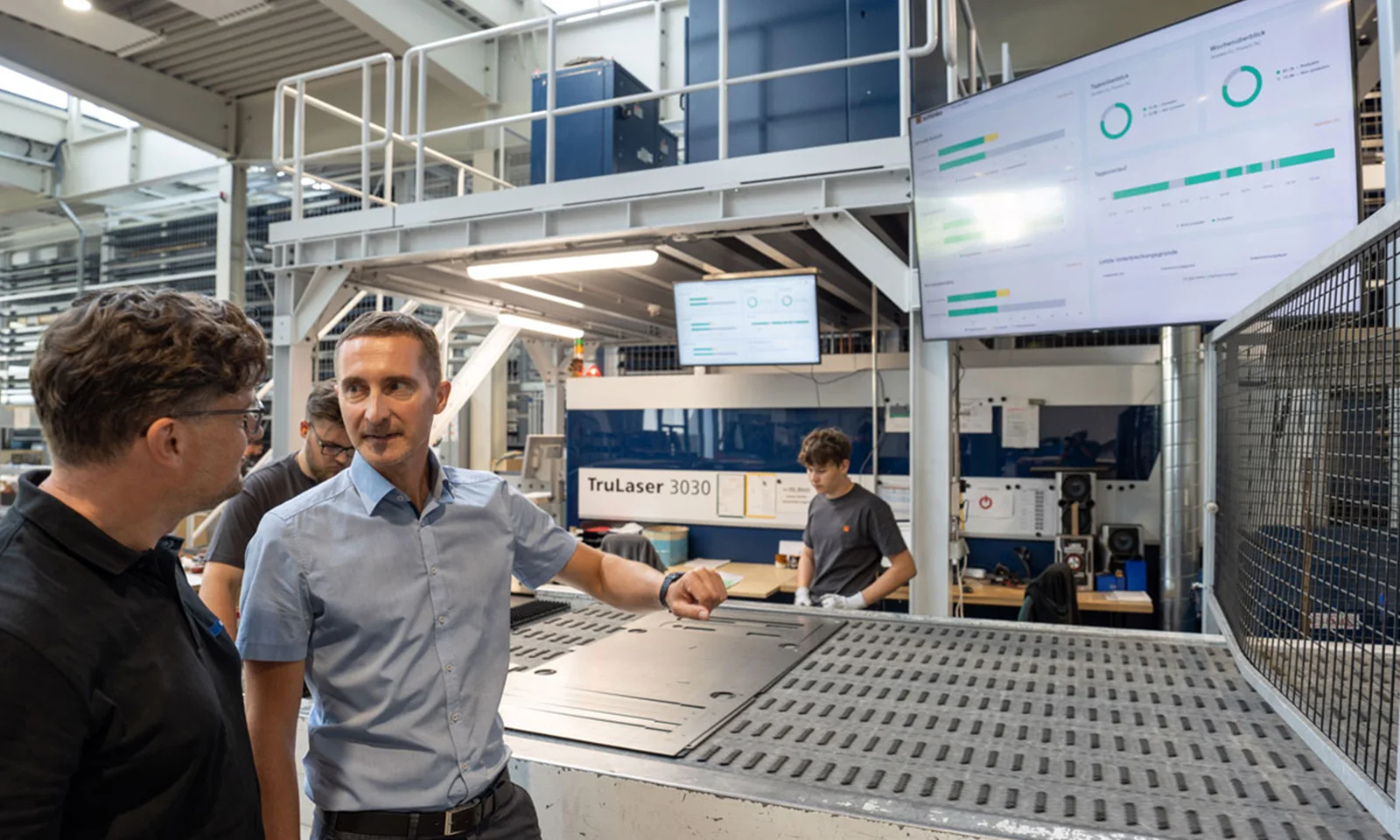
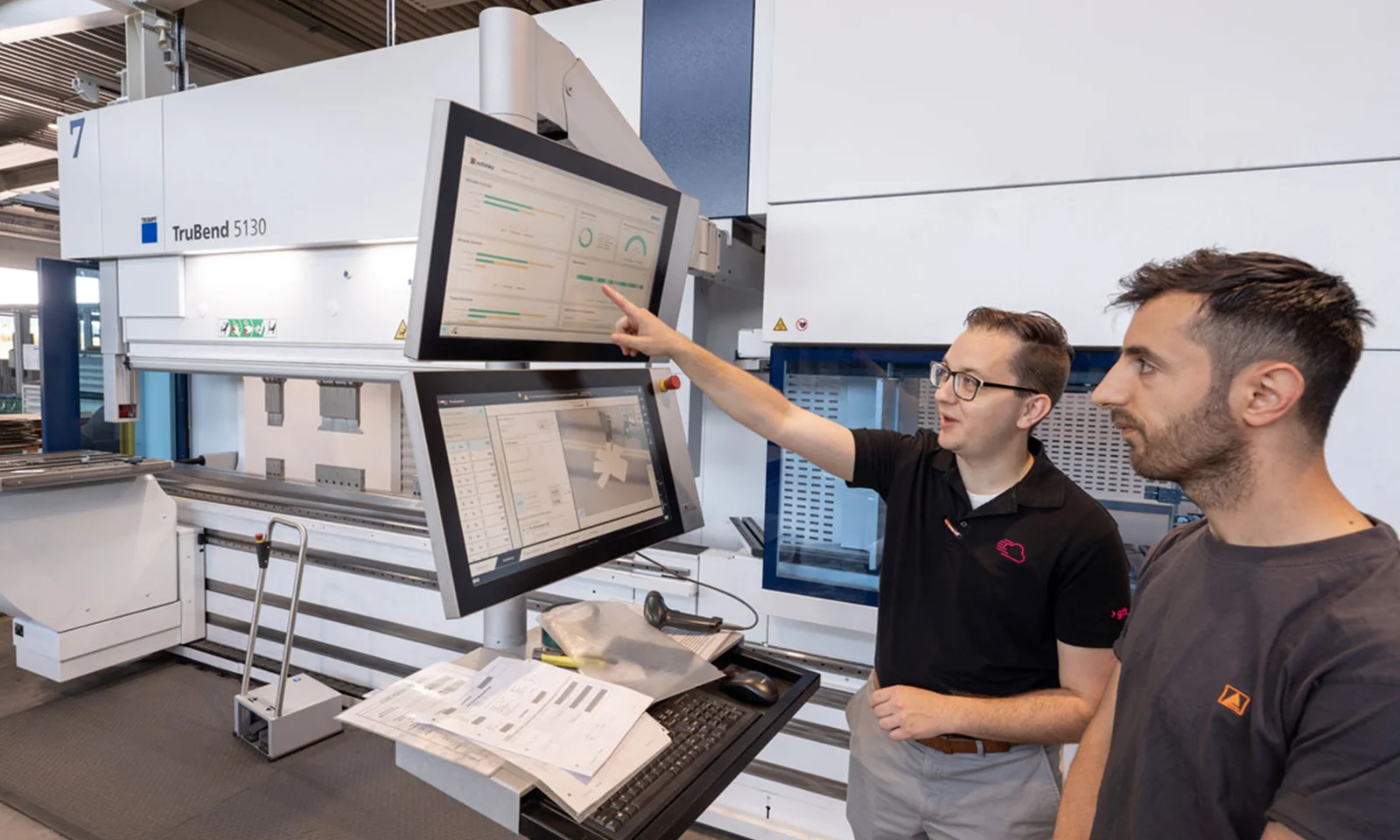
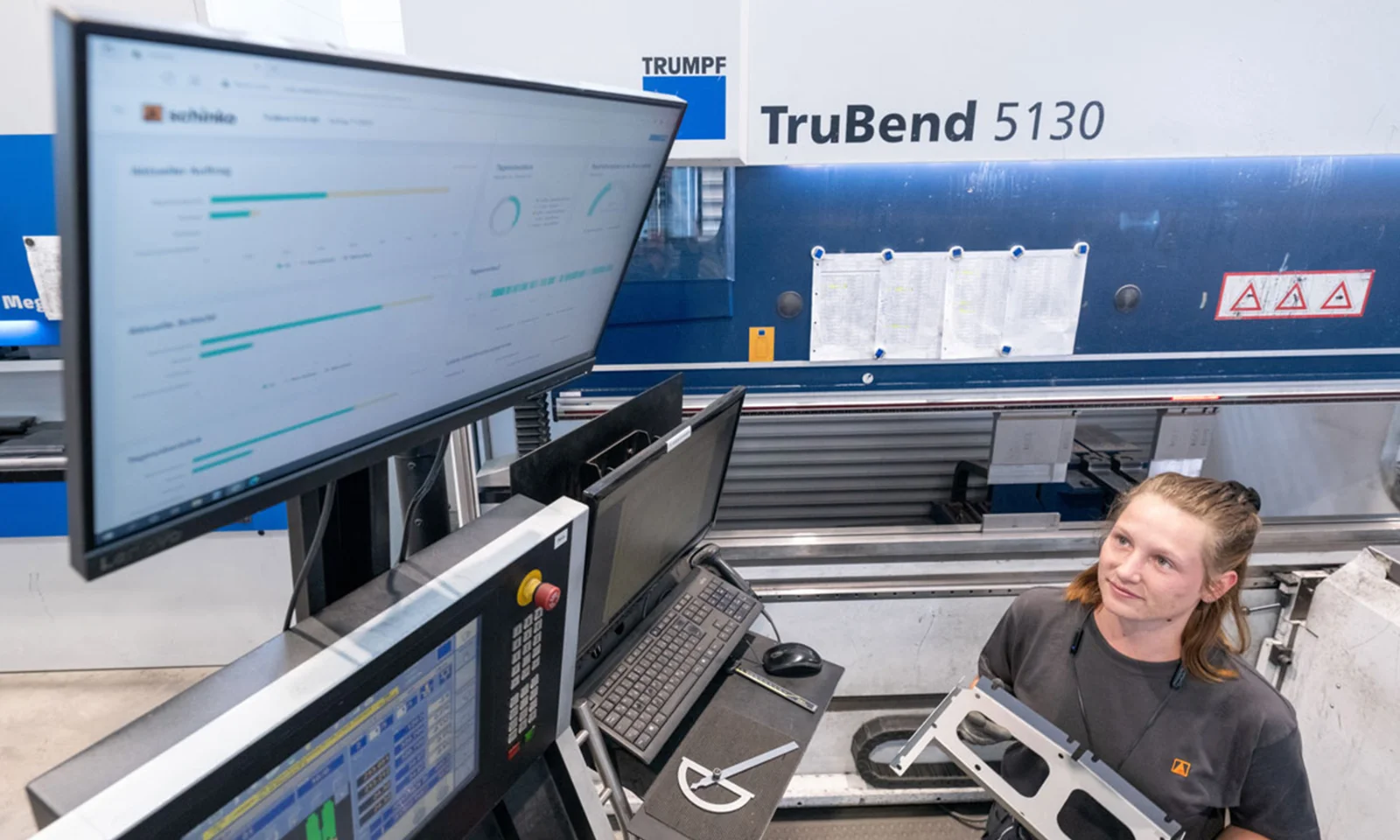
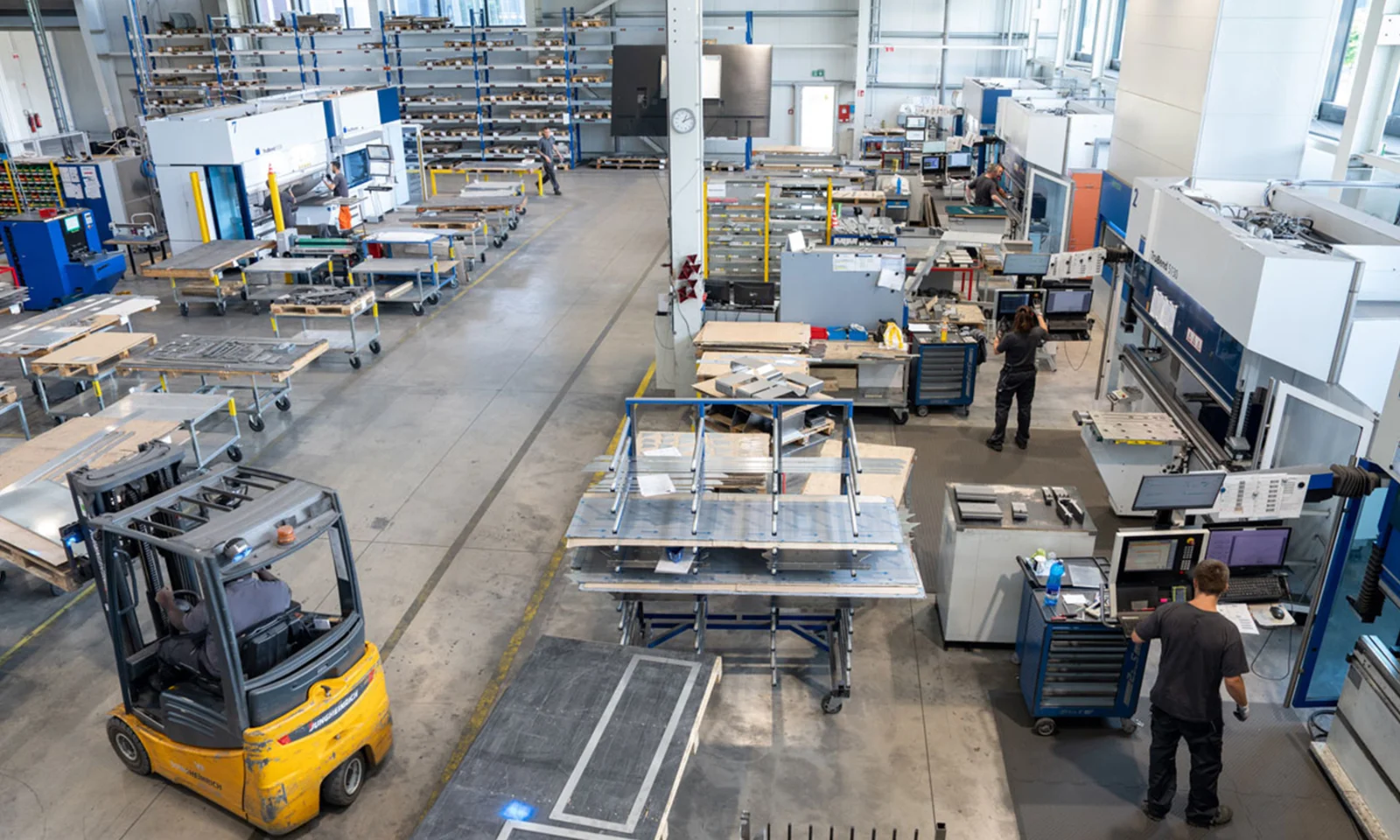
First, the GFT experts developed a procedure for sections of the cutting and edging areas. After a successful test run, GFT's shop floor management system was introduced across the board. It is based on GFT's own Logical Twin Platform SPHINX OPEN captures all available machine data and makes it available to the production team in real time on clear dashboards. In detail, this involves the following information:
- Machine running times (productive, standby, set-up, faults),
- Reasons for faults,
- Materials,
- Employee times per job – always with target and actual status.
Coating came next. Here, interpreting the data, mapping it to process performance and defining the appropriate KPIs was more challenging than in cutting, partly because corona made on-site visits impossible. The GFT team, therefore, had to interatively develop the perfect dashboard that would optimally represent reality and performance. It records all parameters, ranging from machine data in nano high-tech coating through to the weight and areas of the individual components. These components are then attached to hooks and automatically moved into the powder coating system via a ceiling track system. The shop floor management system can then also be used here as large monitors.
“The whole thing gets the team thinking about performance and competitiveness – and we clearly see this in increases in productivity.”
Benefit
Increased motivation and productivity
Motivation and a willingness to optimise have increased since employees have had transparency on pending and completed orders, machine status and achieving their own targets. More importantly, Schinko has also been able to increase cutting productivity by 20%. In bending, where shop floor management is even newer, the increase is currently 10% and, according to plant manager Christian Deinhofer, will increase to more than 20% in the future. He also sees the following advantages:
-
Data can be viewed by all employees via a central dashboard, on all PCs and mobile devices in the company
-
Reaction times are shortened through production monitoring in real time, instant transparency on actual and target times regarding order processing
-
Planning and scheduling are improving constantly thanks to precise key figures and automated reporting
-
Quality and safety increase as faults are detected more quickly and interruptions to operations are reduced in the long term
“We are gradually digitizing in a careful and measured way – with a clear view of costs and benefits at the end of each milestone. When all production areas have been digitized by next year, we will consider the next step forward.”
Download – just one click away
-
Success story
Schinko boosts productivity by 20%
Outlook
Schinko currently operates the GFT system on-premises, i.e. entirely in its own data center. A move to the cloud is not yet an issue for Plant Manager Deinhofer and Managing Director Lengauer. However, both are keeping their eyes open on current developments in cloud services in the manufacturing sector. They are counting on GFT for advice.
As a partner to all major cloud providers, GFT has great expertise in this area and is a development partner to Google and Co. in numerous areas. The company's own software platform SPHINX OPEN, a central data model for Industry 4.0 applications, is also cloud-capable. With more computing power, entirely new applications would be conceivable at Schinko, such as the use of artificial intelligence for detecting discrepancies in quality control.