- Entdecken Sie unser Branchenwissen
- Projektreferenzen
- Vernetzter Maschinenpark für einen Anbieter von Metall-Systemlösungen
Vernetzter Maschinenpark für einen Anbieter von Metall-Systemlösungen
Die Effizienz steigt durch die Auswahl der richtigen Software nach Analyse der Prozesse durch erfahrene Berater*innen. Das wiederum verbessert die Produktivität und spart langfristig Zeit und Geld.
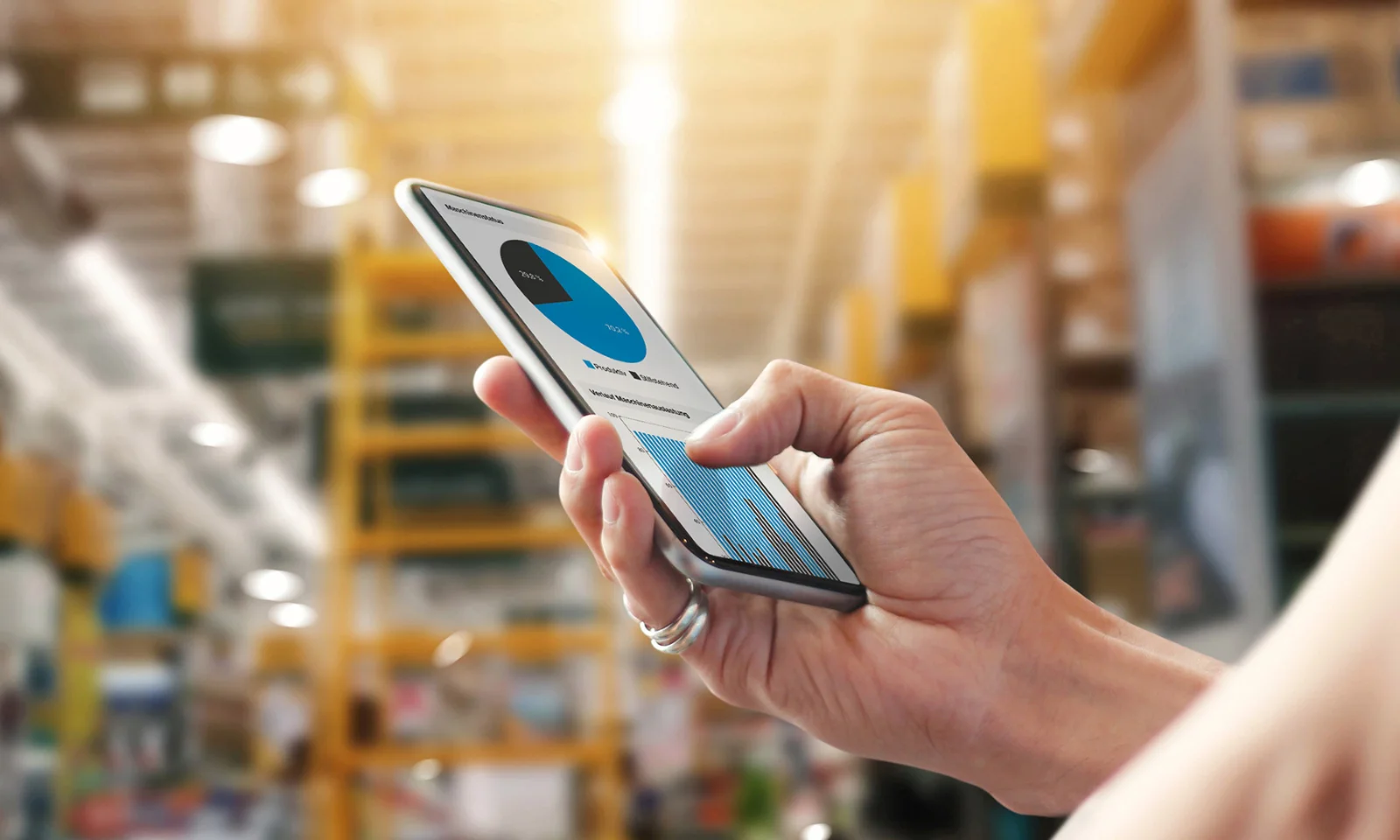
Produktivitätssteigerung
Reduzierung von Lagerbeständen
Digitalisierte Fertigungsprozesse
Optimierung der Liefertreue durch höhere Transparenz
Verbessertes Shopfloor-Management
Zugriff auf Echtzeitdaten über Dashboards
Herausforderung
Mangel an Transparenz und Flexibilität, Kapazitätsengpässe in der Fertigung
Volle Auftragsbücher und voll ausgelastete Maschinen: Für ein mittelständisches Unternehmen klingt das nach einem Traumszenario, besonders in der sehr wettbewerbsintensiven metallverarbeitenden Industrie.
Allerdings haben sich die Anforderungen der Kunden in den vergangenen Jahren massiv geändert. Heute werden kleine Stückzahlen von flexiblen, agilen Lieferanten benötigt, die nicht nur zuverlässig sind, sondern auch genau die richtigen Fertigungsmöglichkeiten aus einer großen Auswahl anbieten. So sah sich unser Kunde, ein KMU, das bereits vielfältige spezialisierte Metalllösungen anbot, durch die neuen Kundenanforderungen zunehmend vor große Herausforderungen gestellt.
Zudem wurde es immer schwieriger, die Fertigung zu steuern. Es war an der Zeit, einige in der Branche wohlbekannte Themen anzugehen:
- Generell fehlende Transparenz in Bezug auf Maschinenstatus und -kapazität
- Unbekannte Fehlerursachen in der Fertigung, die zu Verzögerungen und Unterbrechungen führten
- Große Bestände an fertigen und halbfertigen Komponenten, die Zeit und Ressourcen in Anspruch nahmen
Das Projekt
Digitalisierung von Fertigungsprozessen
Die Umsetzung von Veränderungen parallel zum normalen Betrieb setzte voraus, dass alle Aspekte sorgfältig bedacht werden. Es war wichtig, nicht nur die in der Vergangenheit versuchten Veränderungen zu erfassen, sondern auch die aktuell möglichen sicheren Korrekturen – plus etwaige künftige Verfahren zur flächendeckenden Digitalisierung von Prozessen.
Im Ergebnis sollte der neue Ansatz zu mehr Transparenz und Effizienz führen, ohne das Rad neu zu erfinden oder alle Maschinen zu ersetzen und die Beschäftigten abzuschrecken.
Hierfür nahm GFT im ersten Schritt eine detaillierte Analyse der aktuellen Situation und der am besten geeigneten Szenarien für die Digitalisierung vor.
Danach wurde ein Maßnahmenprogramm evaluiert und beschlossen: Eine Mischung aus neuen Systemen und Nachrüstlösungen, die nicht nur die kurz- und langfristige Implementierung erleichtern, sondern auch den Weg für kontinuierliche Verbesserungsprozesse und die verstärkte Einbindung der Beschäftigten ebnen würden.
Dazu zählten:
- Einführung eines Systems zur herstellerunabhängigen Vernetzung von Maschinen (sowohl Maschinen mit digitalen Schnittstellen als auch Nachrüstlösungen für ältere Maschinen)
- Vernetzung von 10 Maschinen über eine offene IoT-Plattform und deren Bereitstellung für alle relevanten Systeme
- Hochmoderne Dashboards zur Anzeige von Maschinendaten aus unterschiedlichen Endgeräten
Vorteil
Langfristige Produktivitätssteigerungen und Transparenz im Fertigungsbereich
Für ein bereits erfolgreiches KMU ist es besonders erfreulich, wenn es durch ein Veränderungsprogramm auf neue Trends und Kundenanforderungen vorbereitet wird.
Über ihre Dashboards konnten die Beschäftigten beobachten, wie die neuen Systeme anliefen. Dabei stellten sie nicht nur einen deutlichen Anstieg der Produktivität fest, sondern auch eine grundlegende Veränderung bei der Systemzuverlässigkeit und Prozesseffizienz:
- Anstieg der Aufträge, die auf Anhieb pünktlich ausgeliefert wurden, um 20 %
- Reduzierung der Durchlaufzeiten im Vergleich zum vorherigen Set-up um 43 %
- 50 % weniger Teile im Lager bzw. halbfertige Komponenten in Wartestellung für die weitere Verarbeitung
Durch Beratung und die Implementierung von Software-Systemen durch die Expert*innen von GFT konnte unser Kunde seinen Fertigungsbereich deutlich transparenter gestalten.
Das Unternehmen verzeichnete in kürzester Zeit eine höhere Kundenzufriedenheit und stellte schnell fest, dass die Kapazitäts- und Produktivitätssteigerung auch Auswirkungen an anderen Stellen hatte:
- Die Beschäftigten in der Fertigung waren zufriedener.
- Es wurde weniger Zeit vergeudet, und die Beschäftigten konnten den Platz in der Fertigung und im Lager effizienter nutzen.
- Verbesserungen konnten von überall aus an unterschiedlichen Geräten in Echtzeit verfolgt werden.
In einem Satz zusammengefasst: Wichtige Routineprozesse funktionierten wieder. Und auch der langfristige Vorteil war klar zu sehen: Das neue Set-up spart Geld.
Download – nur einen Klick entfernt
-
Projektreferenz
Vernetzter Maschinenpark bei einem Anbieter von Metall-Systemlösungen